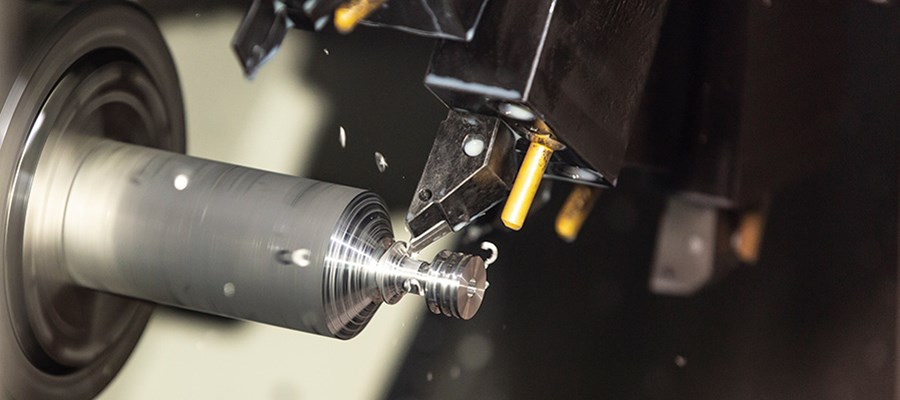
Ең алдымен титан қорытпасын өңдеудің физикалық құбылысы туралы айту керек.Титан қорытпасының кесу күші бірдей қаттылығы бар болаттан сәл ғана жоғары болса да, титан қорытпасын өңдеудің физикалық құбылысы болатты өңдеуге қарағанда әлдеқайда күрделі, бұл титан қорытпасын өңдеуді қиындатады.
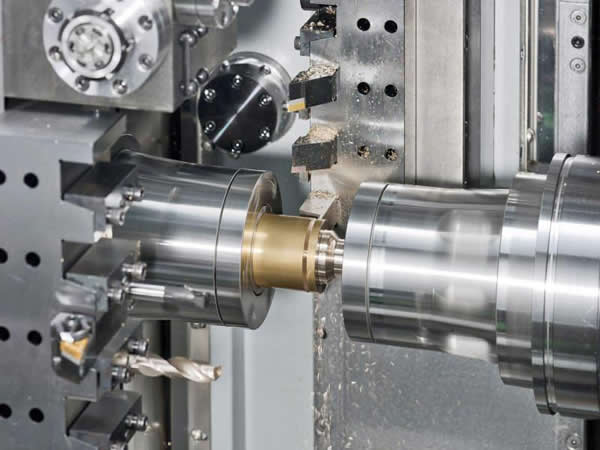
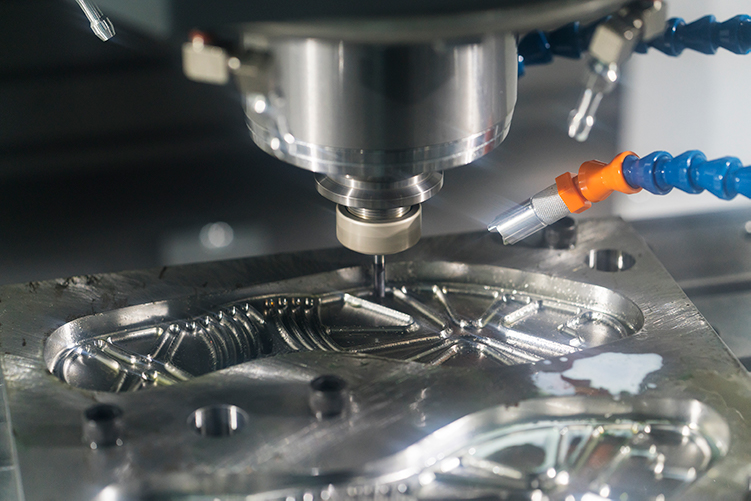
Көптеген титан қорытпаларының жылу өткізгіштігі өте төмен, тек 1/7 болат және 1/16 алюминий.Демек, титан қорытпаларын кесу процесінде пайда болатын жылу дайындамаға тез берілмейді немесе жоңқалар алып кетпейді, бірақ кесу аймағында жинақталады және түзілетін температура 1 000 ° C немесе одан жоғары болуы мүмкін. , бұл құралдың кесу жиегінің тез тозуына, жоңқалануына және жарылуына әкеледі.Жинақталған жиектің қалыптасуы, тозған жиектің тез пайда болуы, өз кезегінде, кесу аймағында көбірек жылу тудырады, құралдың қызмет ету мерзімін одан әрі қысқартады.
Кесу процесінде пайда болатын жоғары температура сонымен қатар титан қорытпасының бөлшектерінің бетінің тұтастығын бұзады, нәтижесінде бөлшектердің геометриялық дәлдігі төмендейді және олардың шаршау беріктігін айтарлықтай төмендететін жұмыстың шыңдалуы құбылысы.
Титан қорытпаларының серпімділігі бөлшектердің өнімділігі үшін пайдалы болуы мүмкін, бірақ кесу процесінде дайындаманың серпімді деформациясы дірілдің маңызды себебі болып табылады.Кесу қысымы «серпімді» дайындаманың құралдан алыстап, секіруіне себепші болады, осылайша құрал мен дайындама арасындағы үйкеліс кесу әрекетінен үлкен болады.Үйкеліс процесі сонымен қатар титан қорытпаларының нашар жылу өткізгіштігі мәселесін қиындата отырып, жылуды тудырады.
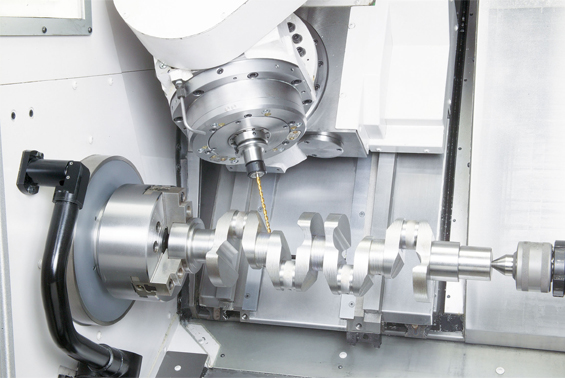
Бұл мәселе оңай деформацияланатын жұқа қабырғалы немесе сақина тәрізді бөлшектерді өңдеу кезінде одан да маңызды.Титан қорытпасының жұқа қабырғалы бөлшектерін күтілетін өлшемдік дәлдікке дейін өңдеу оңай жұмыс емес.Өйткені дайындаманың материалы аспаппен итерілгенде, жұқа қабырғаның жергілікті деформациясы серпімділік шегінен асып кетті және пластикалық деформация пайда болады, ал материалдың беріктігі мен кесу нүктесінің қаттылығы айтарлықтай артады.Бұл кезде бұрын анықталған кесу жылдамдығымен өңдеу тым жоғары болады, бұл одан әрі құралдың күрт тозуына әкеледі.«Жылу» титан қорытпаларын өңдеуді қиындататын «түбірлік себеп» деп айтуға болады.
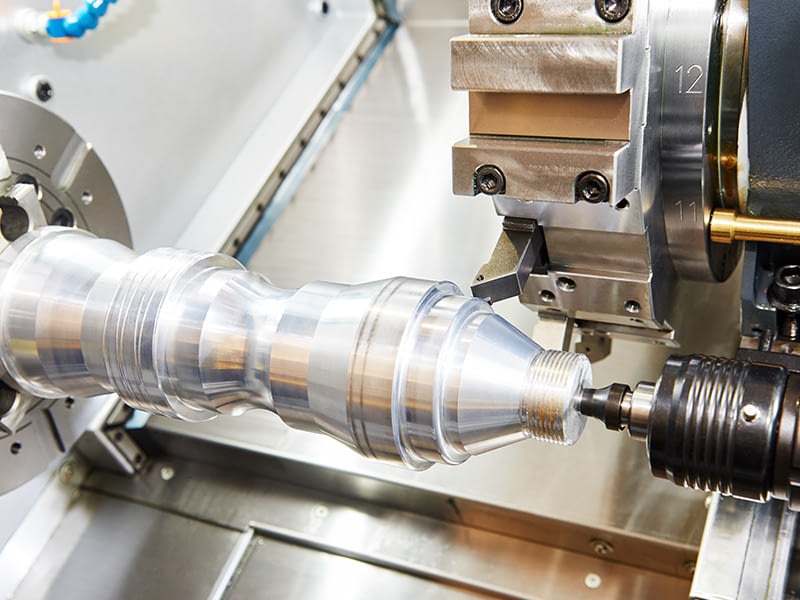
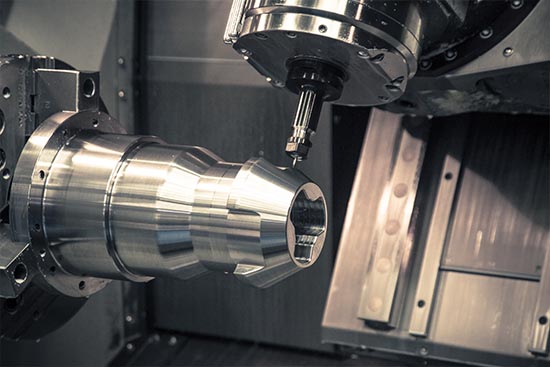
Кесетін құрал индустриясының көшбасшысы ретінде Sandvik Coromant титан қорытпаларын өңдеу бойынша технологиялық ноу-хауды мұқият құрастырып, бүкіл саламен бөлісті.Сандвик Коромант титан қорытпаларын өңдеу механизмін түсіну және өткен тәжірибені қосу негізінде титан қорытпаларын өңдеудің негізгі технологиялық ноу-хау келесідей екенін айтты:
(1) Оң геометриялық кірістірулер кесу күшін, кесу жылуын және дайындаманың деформациясын азайту үшін қолданылады.
(2) Дайындаманың қатаюын болдырмау үшін тұрақты беруді ұстаныңыз, кесу процесінде құрал әрқашан беру күйінде болуы керек, ал радиалды кесу мөлшері ae фрезерлеу кезінде радиустың 30% болуы керек.
(3) Жоғары қысымды және үлкен ағынды кесу сұйықтығы өңдеу процесінің термиялық тұрақтылығын қамтамасыз ету және шамадан тыс температура салдарынан дайындама бетінің азғындауын және құралдың зақымдалуын болдырмау үшін қолданылады.
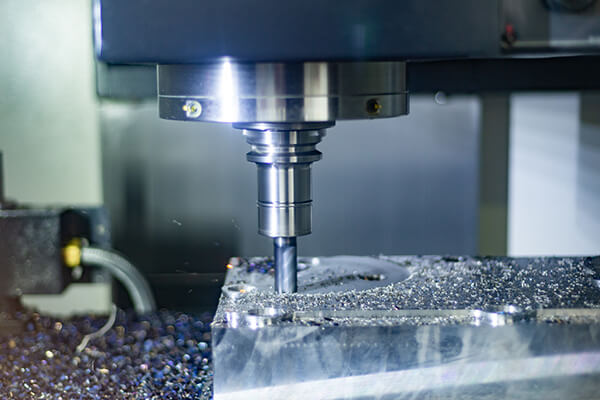
(4) Пышақтың жиегін өткір ұстаңыз, өткір құралдар қызып кетудің және тозудың себебі болып табылады, бұл құралдың оңай істен шығуына әкелуі мүмкін.
(5) Титан қорытпасының барынша жұмсақ күйінде өңдеу, өйткені шынықтырудан кейін материалды өңдеу қиынырақ болады, ал термиялық өңдеу материалдың беріктігін арттырады және ендірменің тозуын арттырады.
(6) Кесу үшін үлкен мұрын радиусын немесе фасканы пайдаланыңыз және кесуге мүмкіндігінше көп кесу жиектерін салыңыз.Бұл әр нүктеде кесу күші мен жылуды азайтады және жергілікті сынуды болдырмайды.Титан қорытпаларын фрезерлеу кезінде кесу параметрлерінің ішінде кесу жылдамдығы құралдың қызмет ету мерзіміне ең үлкен әсер етеді vc, одан кейін радиалды кесу мөлшері (жонғылау тереңдігі) ae.
Жіберу уақыты: 06 сәуір 2022 ж